While tourism, resources and education usually dominate trade between Asia and Australia, a surprising new trade has been flourishing under the radar in recent years – the booming business of prefabricated “prefab” housing and building materials.
Though the numbers may pale in comparison to the billions of dollars in two-way trade between the regions, Australian imports of prefab goods from Asia have been steadily climbing year over year.
Chinese prefab exports dominate the market, followed by those from Vietnam and Malaysia, mirroring patterns seen in broader construction material imports such as steel.
As Australia grapples with a housing affordability crisis, prefab housing has emerged as one potential solution to increase housing supply. Experts say imports of prefab components from Asia and elsewhere are likely to continue climbing to supplement locally-made materials.
This push towards prefab – assembling modular and stand-alone parts manufactured off-site into full homes – comes as the housing shortage has rocketed to the top of the national agenda. With the cost of living crisis as a backdrop, housing affordability has become a crucial issue ahead of next year’s elections.
More and more people are talking about prefab in an Australian context
“There’s no doubt that the electorate’s mind is focused on cost of living issues with housing at its root,” said Matthew Kandelaars, Property Council of Australia’s group executive on policy and advocacy. “More and more people are talking about prefab in an Australian context, given the significant national housing supply deficit that we’re facing.”
A strong trading relationship with China and other parts of Asia will remain crucial, given the pivotal role these markets play in Australia’s housing landscape. Experts note that foreign buyers from Asia – who are limited to purchasing new homes – provide vital impetus for the construction of additional housing stock, in addition to supplying essential building materials.
“As Australia’s domestic sector for prefab housing … [and supply chains] prove themselves up and scale up, then the natural position would be that we would look to import what we can,” Kandelaars said.
Over the past five years, Australia has imported nearly A$500 million (US$338 million) worth of prefab housing materials and modules from China alone, while imports from Malaysia and Vietnam each totalled around A$34 million.
Chinese goods made up roughly 70 per cent of Australia’s prefab imports last year – dwarfing the more modest 3 per cent shares from Malaysia and Vietnam, in distant second and third place.
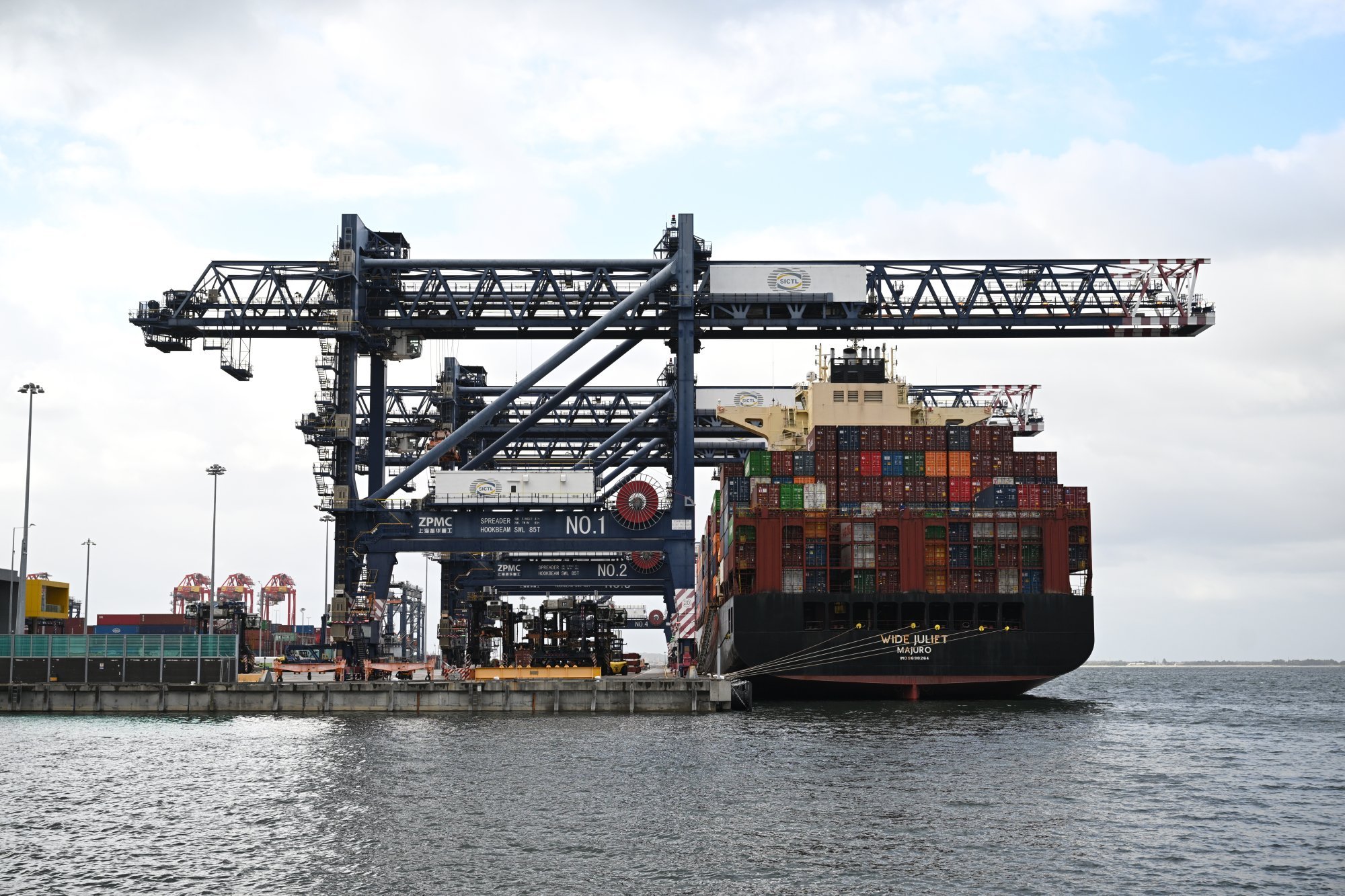
This surge in Asian imports comes as the Australian government has set an ambitious target – signing a new national housing accord with state counterparts to build 1.2 million new homes between 2024 and 2029. National statistics show just over 900,000 dwellings were constructed nationally in the previous five-year period.
Kandelaars highlighted the scale of the challenge, citing a complex and bottlenecked housing system beset by rising taxes, high construction and land costs, and cumbersome development approval red tape. He said that while the “dream of a quarter-acre block that has been hard-wired into the Australian psyche for so long is changing”, the planning system hasn’t shifted as quickly.
But he said Australia had reached a tipping point, with lawmakers now accepting the reality that the country’s housing affordability woes are “intrinsically” linked to persistently low new home-supply levels.
The path to this point has not been without its challenges, however. Fingers have frequently been pointed at foreign buyers, particularly those from China, for allegedly jacking up housing demand and prices. Yet research has shown that foreign-buyer demand actually provides a crucial business case for new housing development, ultimately benefiting Australian residents.
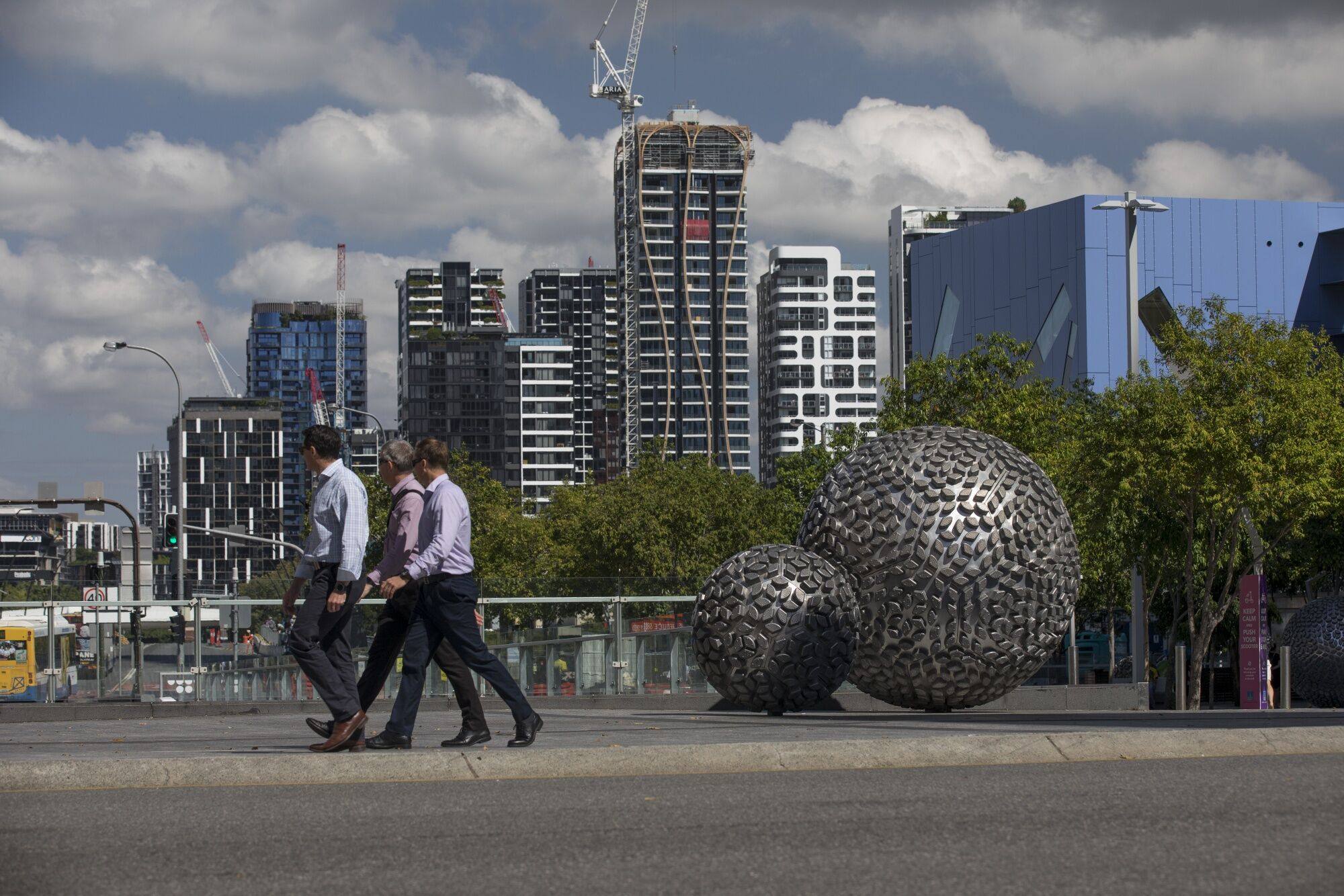
As Australia has sought solutions, “smart building” groups like prefabAus, the country’s pre-eminent prefab industry body, noted that the new national housing accord and other manufacturing plans presented significant opportunities for the prefab sector to help deliver new homes.
Australia’s building ministers echoed this sentiment, earlier this year agreeing to cut red tape on construction codes to permit greater use of prefabricated and modular construction techniques.
Businesses are seizing these openings, with Damien Crough, founding director of prefabAus, reporting a surge in inquiries from prefab material suppliers in China, Vietnam, and Thailand seeking to join the association, alongside local prefab builders.
Private Australian developers and entrepreneurs also told This Week in Asia that they are exploring options to source materials, primarily from China and Vietnam, and invest in prefab development ventures.
The fact is that Australia struggles to meet its housing needs domestically
One Australian entrepreneur based in Vietnam said he was in the process of securing Vietnamese-made materials, but acknowledged the high certification standards in Australia for housing made it challenging to import Asian-made products, even though manufacturing costs were lower and lead times faster in Asia.
Similarly, a Malaysian developer based in Sydney lamented that the prefab industry could have achieved much greater scale, beyond “just replacing holiday cabins in caravan parks”, were it not for the difficulty in meeting Australia’s stringent building and material standards.
Both individuals declined to be named, as they are working on commercially sensitive deals.
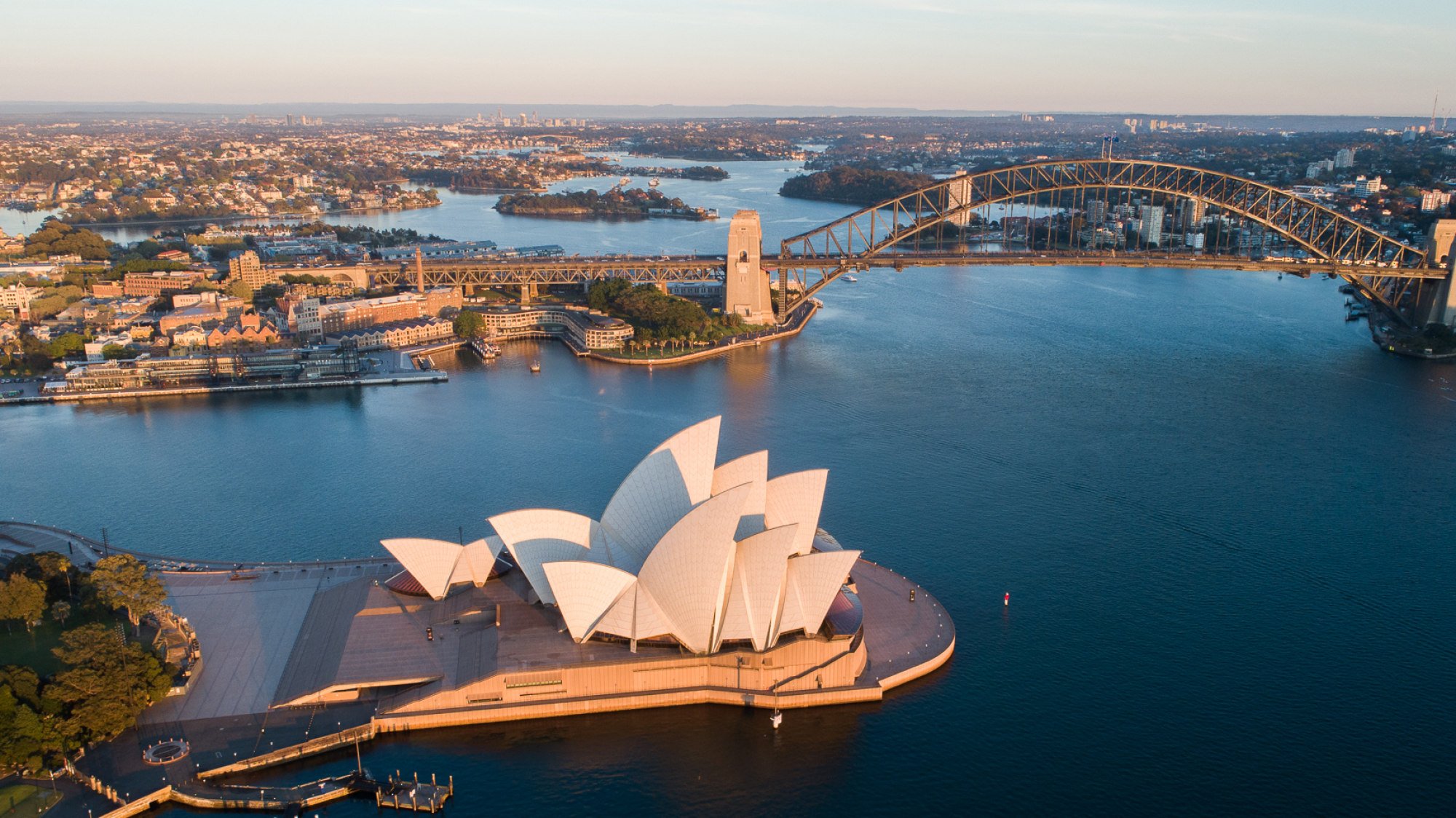
Pushback on Chinese products
Aside from compliance issues with quality standards and building codes, Crough of prefabAus said there were concerns that materials imported from overseas, such as Asia, may not be properly inspected for quality or could be damaged in transit to Australia.
Indeed, it is not uncommon to see Ikea-style, click-together home kits being sold on Asian e-commerce platforms, with prospective buyers questioning their quality online.
To tackle these obstacles, builders like Bibo Build – which currently puts together bespoke prefab “Lego-style kits” known as packs and produces assembly blueprints for builders, but hopes to scale up to larger projects – have taken matters into their own hands. Bibo manufactures Chinese products locally and supervises the entire production process to ensure the materials comply with Australian standards before being shipped.
Bibo founder Lina He told This Week in Asia there was “resistance” to prefab products from overseas, including Asia.
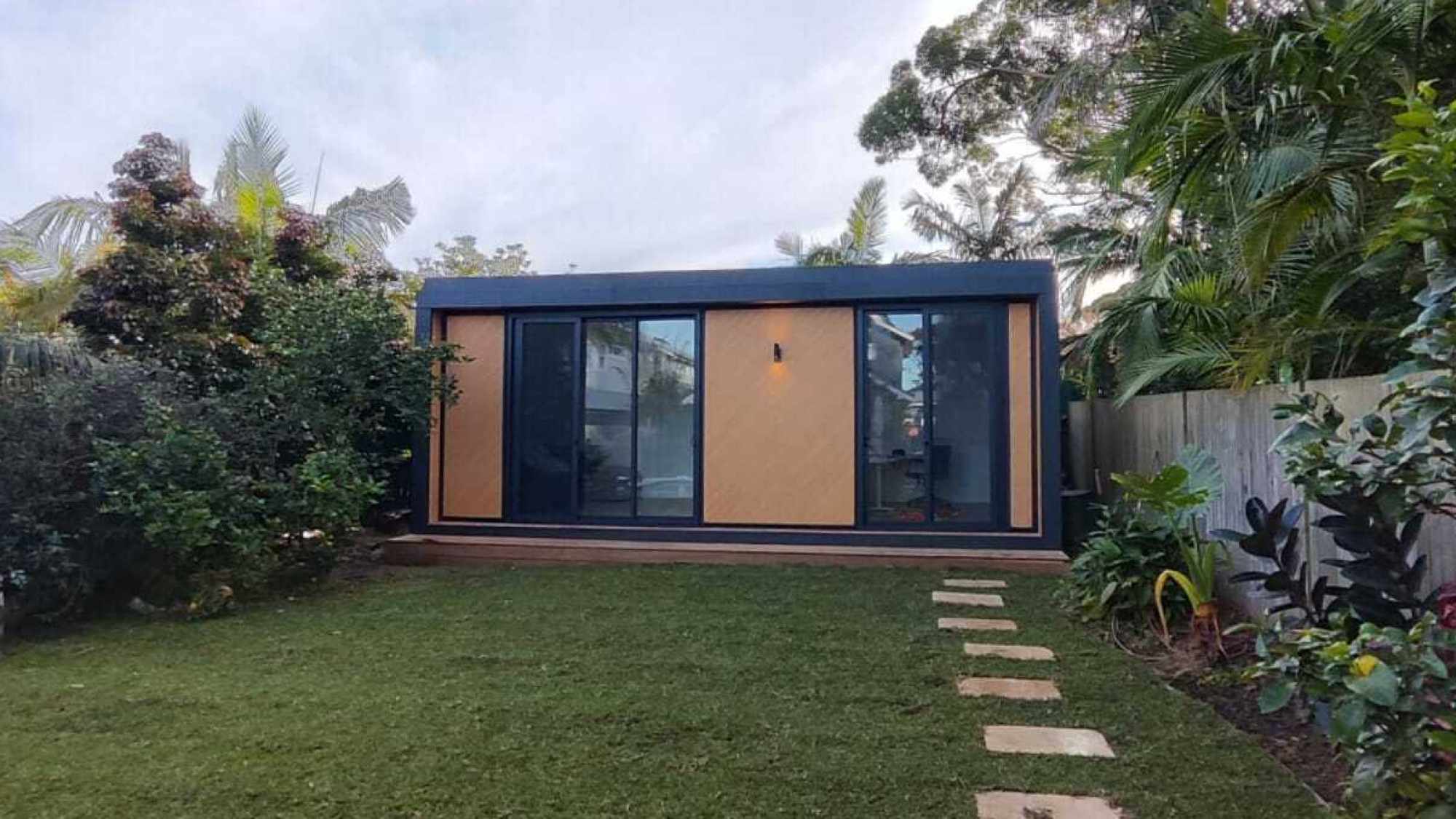
“With [so] many made-in-Australia campaigns, it doesn’t really help, but on the other hand, there is a genuine lack of [affordable] solutions,” He said. “So, some people are more practical about it.”
According to He, making prefab “packs” remains cost-prohibitive within Australia, as the domestic supply chain lacks depth and manufacturing lead times are too long. The speed and cost advantages of Chinese production offset the additional compliance work needed to certify these imports for the Australian market.
Resisting prefab products made in China or elsewhere, He argued, does not make practical sense, as many buildings in Australia already utilise hybrid construction involving prefab components like drop toilets or panels imported from China and other countries. In fact, Australia imports most of its housing construction materials, of which an estimated 60 per cent come from China.
When it comes to prefab manufacturing and building, China actually has a better track record than Australia, with 6 per cent of houses currently built off-site and plans to increase this to 10-15 per cent driven by a domestic “green push”, according to prefabAus. In contrast, only around 5 per cent of Australian homes are currently constructed using prefab methods. However, both countries lag behind Scandinavian nations, which are the market leaders.
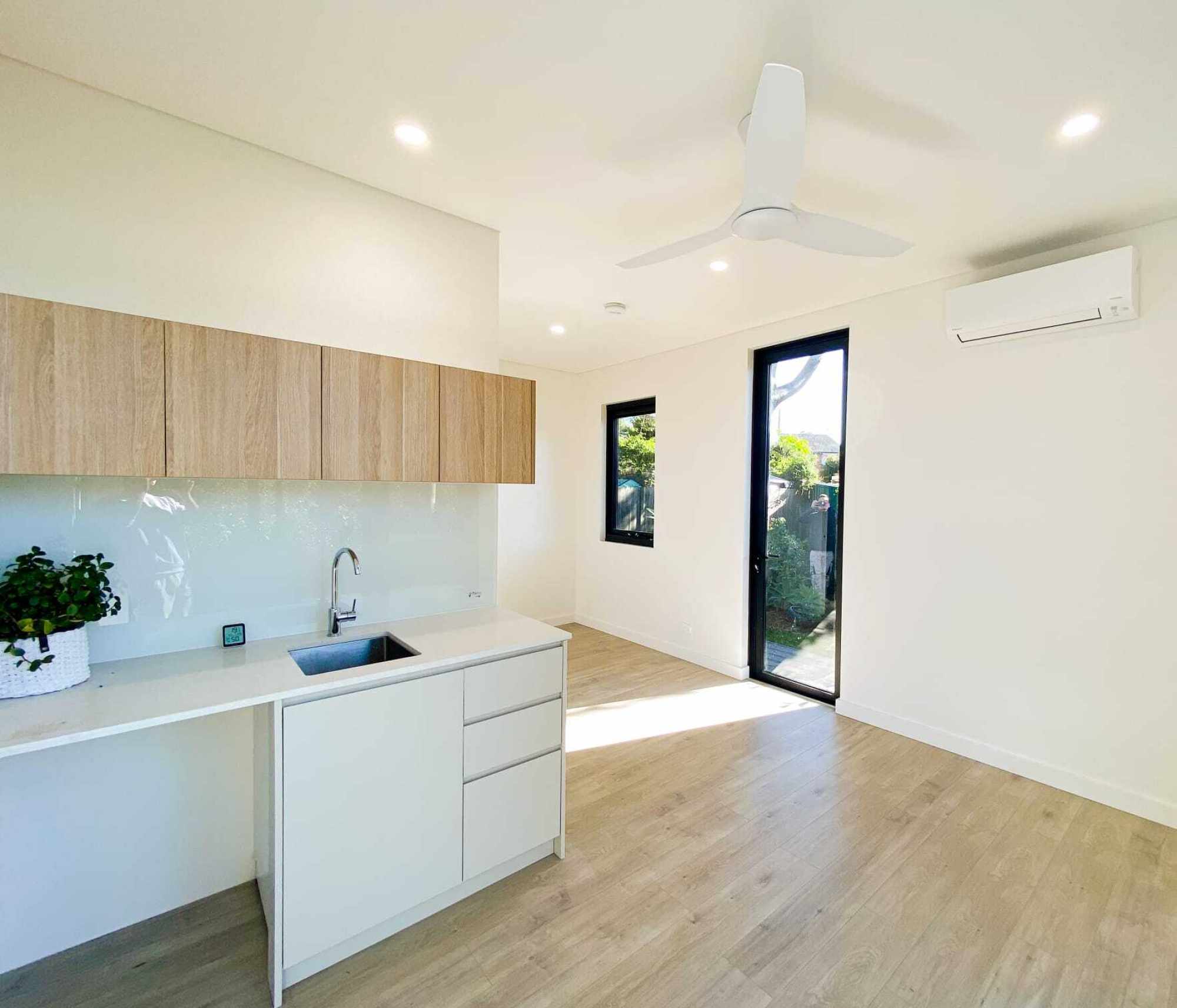
Economist James Laurenceson, director of the Australia-China Relations Institute, believes prefab housing could present an opportunity for increased trade between the two countries.
“The fact is that Australia struggles to meet its housing needs domestically, and no other country can supply prefab materials at a quality and price point like China can,” he said.
“Robust trade with China in the form of prefab materials will be a key factor that improves housing affordability in the coming years.”
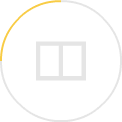