An ancient technique, famously used 2,500 years ago to make a sword for a legendary Chinese king, has now been used for a tunnel boring machine known as the “king of construction machinery”.
While trying to create the world’s largest piece of equipment for tunnel construction, scientists and engineers on the project had to overcome one major hurdle: no country had ever been able to create steel strong enough for the massive machine.
The tunnel boring machine (TBM) has a main bearing with a diameter of 8.61 metres (28 feet) – as tall as a three-storey building. This bearing drives the giant machine that weighs over 10,000 tonnes – about as heavy as the Eiffel Tower.
All this load is borne by the surface layer of the bearing which is less than 1cm (0.4 inch) thick.
The main problem with manufacturing a bearing of that size is that the temperatures of the different areas change at different speeds during the process, and this lack of uniformity can make the steel weak.
For an answer to this modern problem, the project team had to look to the past.
A technique used in making the 2,500-year-old “Sword of Goujian” offered a solution, according to a report from the state-run Science and Technology Daily on Tuesday.
Known for its unusual sharpness and intricate design, the bronze sword was excavated from an ancient tomb in Hubei province in 1965. It is believed the original owner of the sword was Goujian, king of Yue from 496BC to 465BC, during the late Spring and Autumn period.
To create his bronze sword, the ancient blacksmiths hardened it using a process called “quenching”. This is where metal is heated to high temperatures, then rapidly cooled in water, gas or other fluids to achieve certain material properties, such as increased hardness.
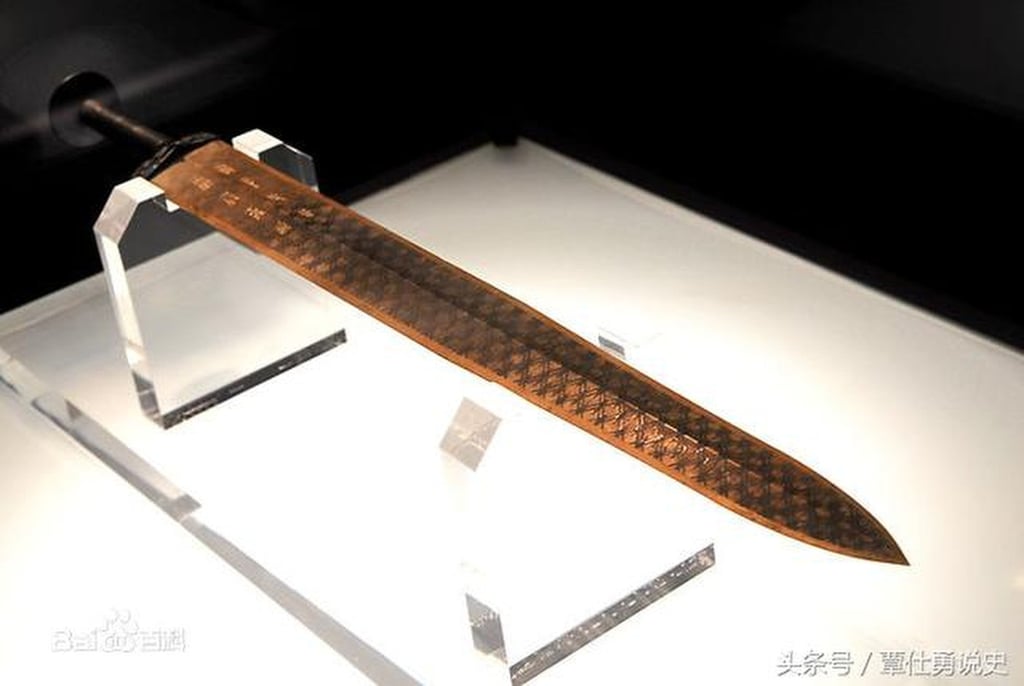
While quenching is common in sword making, the Chinese blacksmiths employed one major difference while forging the Sword of Goujian: they covered it with clay during the quenching process so that the temperature of each part of the sword changed uniformly.
Using clay as a medium for the TBM bearing “perfectly solved” the problem of uneven quenching temperatures, according to the project team.
Tunnel boring machines are widely used in underground construction. They are capable of cutting through all kinds of materials and terrains, from soft clay to the hardest granite – but this depends on the main bearing.
Previously, the largest TBM main bearing had a diameter of just under 8 metres, and set a world record when it was built in 2021. It was manufactured by Liebherr, a German-Swiss multinational equipment manufacturer based in Bulle, Switzerland.
Now that record has been eclipsed by the bearing built by the China Railway Construction Heavy Industry Corporation Limited (CRCHI) last October.
And on Tuesday, the project team led by Xie Jindong told Science and Technology Daily how they overcame their major technological challenges to build the “king of construction machinery”.
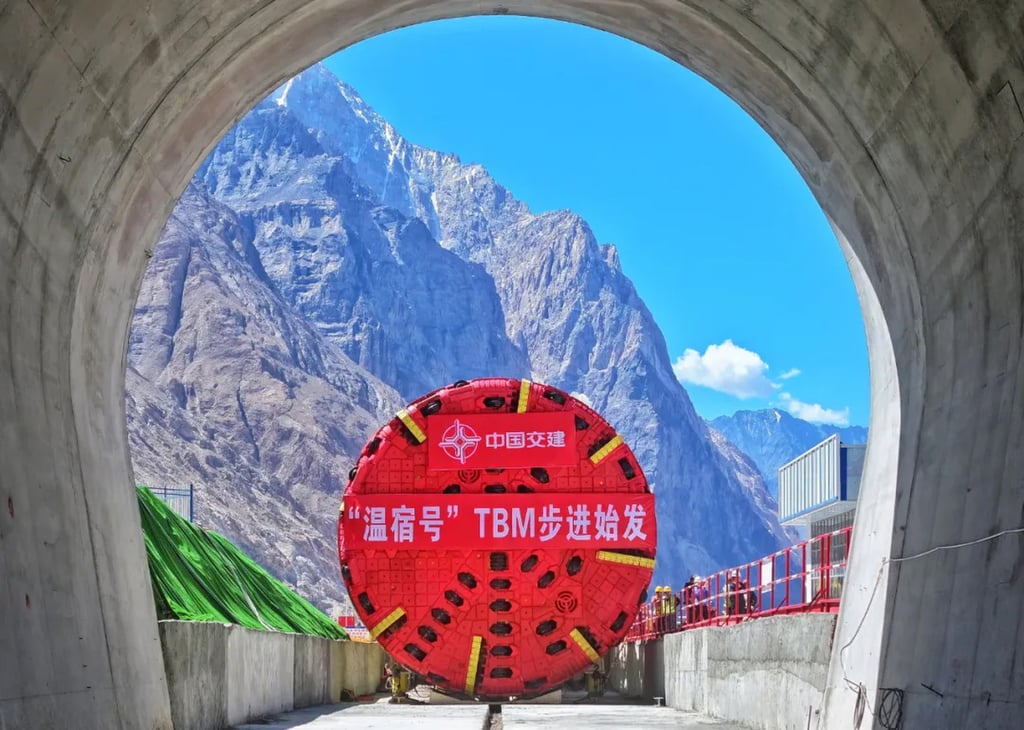
With more than 30,000 parts and components, the TBM can be seen as a benchmark for measuring a country’s strength in producing underground construction machinery.
While such equipment has been developed and used in the West for more than 100 years, China still relied on imports until the beginning of the 21st century – with high purchase and maintenance costs.
China produced its first domestic machine in 2008, and since then has continued to make technological breakthroughs while rapidly gaining global market share.
Back in 2009, almost 95 per cent of the machines in China were imported, but by 2017, the production and sales of Chinese-built TBMs had already topped the global market.
TBMs combine multiple technologies including machinery, electronics, information technology, and artificial intelligence.
In 2019, the Communist Party-run newspaper Guangming Daily praised TBMs as another major accomplishment for China’s high-end intelligent manufacturing equipment.
However, despite these successes, China had yet to achieve self-reliance in making the main bearings for TBMs.
In July 2019, CRCHI decided to establish a research and design institute to address this issue. The following year, the Chinese Academy of Sciences also launched a joint R&D project to achieve independent manufacturing of high-end bearings.
With the debut of this record-sized bearing, CRCHI said China can stake its claim as a world leader in extra-large-diameter main bearings.
In a statement, the company said that the project team had “finally overcome manufacturing difficulties through hundreds of experiments with various processes and materials, enabling the bearing to have a long service life and high manufacturing precision”.
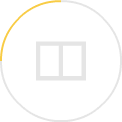